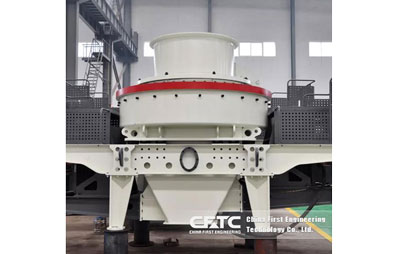
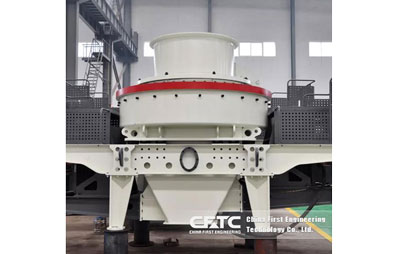
Sand making machine
Feed particle size30-60mm.
Processing capacity10-500t/h.
Applicable materialRiver pebble, granite, basalt, iron ore, limestone, calcite, quartz, abrasive, concrete aggregate, etc..
Sell Hot: South Africa, Nigeria, Kenya,Mexico, Uzbekistan, Chile, Tanzania, Peru, Brunei, Brazil, Iran, Philippines, Malaysia, Vietnam, Pakistan, India, Russia, Venezuela, USA, etc.
free delivery this machine related parts!
The sand making machine is also called impact crusher. The scope of application is: expressway, high-speed railway, high-rise building, municipal, hydropower dam construction, concrete mixing station, sand and gravel yard. This series of sand making machine is suitable for the crushing and shaping of soft, hard, medium and hard materials. It can be widely used in various ores, rocks, cement, refractory materials, aluminum soil, silicon carbide, glass raw materials, infrastructure stone, various types. The processing of slag and other materials, especially for river pebbles, pebbles, limestone, quartz, granite and other materials, is particularly good, and the equipment output and finished product quality are widely praised by users! The mechanism produced by the sand making machine is beautiful in sand type and reasonable in grading, and is extremely suitable for sand for construction and gravel for road construction.
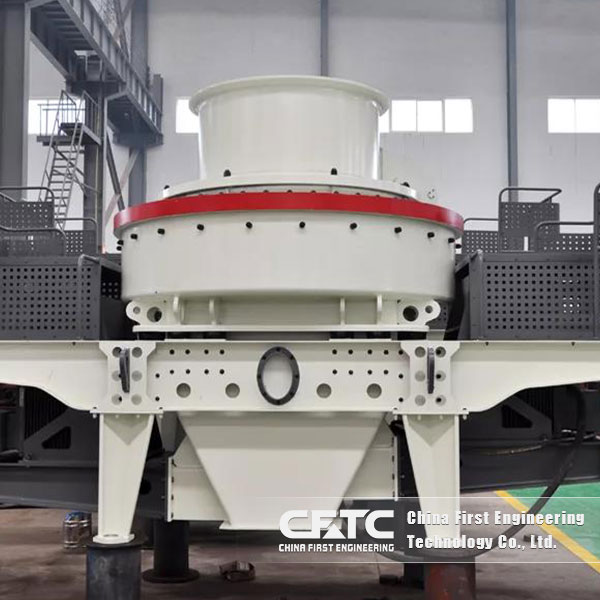
The sand making machine is mainly composed of seven parts: feeding, distributor, vortex breaking chamber, impeller experience, spindle assembly, base transmission and motor.
Sand making machine performance advantage
Less wear and durability
During the sand making process, the stone material can form a protective bottom layer, and the materials are crushed and broken by themselves, and are not directly in contact with the metal components, but are impacted, rubbed and pulverized with the material lining, thereby reducing the wear of the equipment and its components.
Significant energy saving and low production cost
The size of the inlet and outlet ports is adjustable, and the materials can be crushed to different extents to reduce energy consumption. After the small materials are processed by the sand making machine, they can become qualified sand and gravel materials without secondary treatment and cost saving.
Unique technology and high wear resistance
The hammer head is made of high-strength steel with high wear resistance. Its impact resistance and toughness are very high. The frame is welded and stable, avoiding large vibrations in the work, low failure rate of the whole machine and long service life. .
Good sealing, no pollution in production
The sealing element adopts water-sealing parts, the structure is reasonable and compact, the gap between the parts is reduced, the dust is prevented from entering, the ingenious air circulation inside the vortex chamber is circulated, the dust is small, the noise is small, and environmentally-friendly green production is realized.
Parameters
Type | input (mm) | power(kw) | speed (r/min) | capacity (t/h) | size(mm) |
CFTC-06 | 30 | 2P 37-55KW | 2000-3000 | 10-30 | 2500×1620×2600 |
CFTC-07 | 45 | 4P 55-75KW | 1500-2500 | 25-55 | 2700×1760×2800 |
CFTC-09 | 50 | 4P 110-150KW | 1200-2000 | 55-100 | 3900×2000×3070 |
CFTC-10 | 60 | 4P 150-180KW | 1000-1700 | 100-160 | 4600×2350×3450 |
type | capacity(t/h) | input(mm) | power(kw) | size(mm) | |
Soft material | Hard material | ||||
TK7809 | 45-115 | <30 | <25 | 4P 90KW | 4000×1970×2250 |
TK7811 | 60-150 | <30 | <25 | 4P 2×55KW | 4000×1970×2250 |
TK8618 | 120-250 | <35 | <30 | 4P 2×90KW | 4300×2340×2790 |
TK8622 | 150-330 | <35 | <30 | 4P 2×110KW | 4300×2340×2790 |
TK9626 | 190-380 | <40 | <35 | 4P 2×132KW | 4750×2555×2960 |
TK9632 | 220-500 | <40 | <35 | 4P 2×160KW | 4750×2555×2960 |
Principle
Sand machine working principle
The material enters the sand making machine from the feeding hopper. The material is divided into two parts by the feeder, and a part enters the high-speed rotating impeller, which is rapidly accelerated, and then ejected from the three flow paths at a speed of 60-70 m/s. Firstly, it is crushed and broken with a part of the material falling from the periphery of the distributor, and then impacts on the material lining in the vortex cavity, rebounds by the material lining, impacts obliquely upward to the top of the vortex chamber, and changes its moving direction. The deflection moves downward, and the material emitted from the impeller flow path forms a continuous material curtain. The crushed material is discharged from the lower discharge port, and the circulating screening system forms a closed circuit. Generally, the material can be broken into 20 mesh or less after three cycles.
During the whole crushing process, the materials are crushed and broken by themselves, not directly in contact with the metal components, but impacted, rubbed and pulverized with the material lining, which reduces material pollution, makes the materials more clean, and reduces the chance of mechanical wear. , extended component usage time. In addition, the inside of the vortex chamber adopts ingenious airflow self-circulation, which eliminates dust pollution and has better environmental protection effect.
Send Enquiry
write down your requirement and contact details in the following form to get the latest price of this product within one day!
Hot Product
Pursuit of excellence, innovation is not limited!